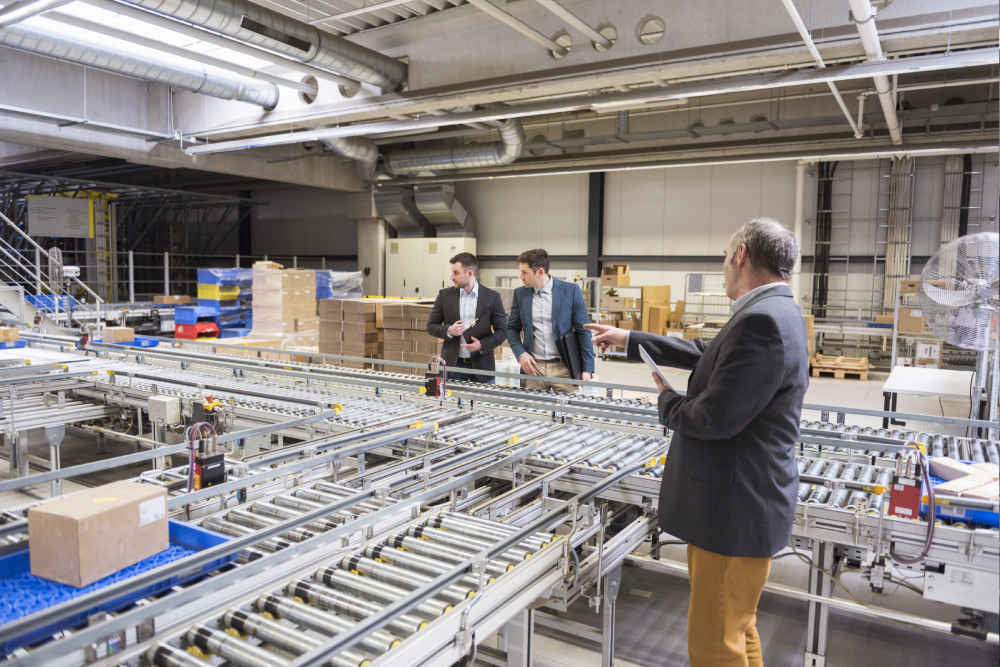
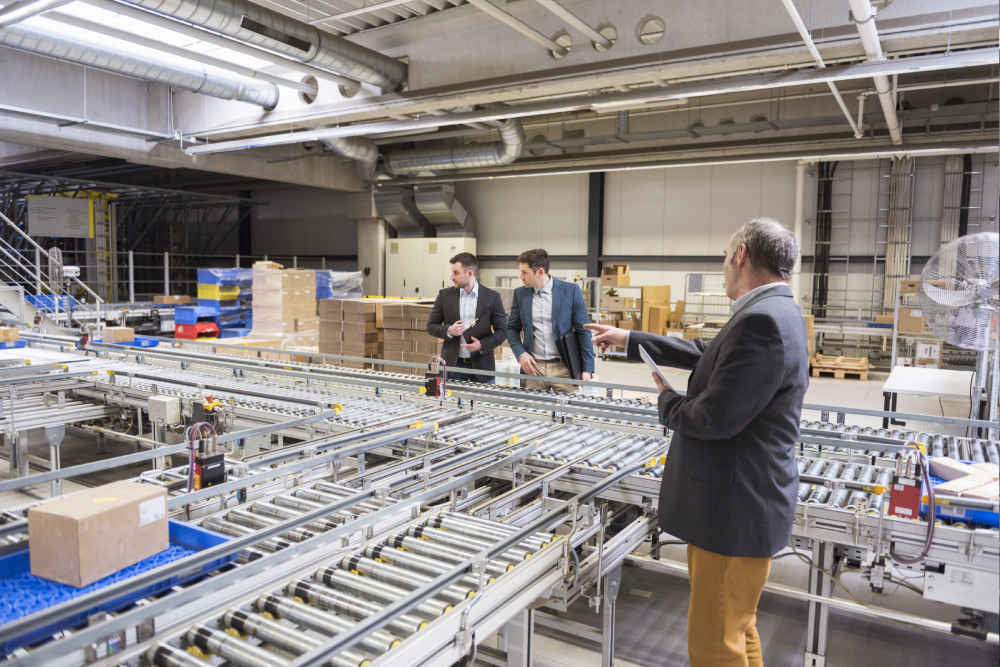
A warehouse operates as a high-energy environment where safety cannot take a backseat. Conveyor systems, with their moving parts and mechanical complexity, are often a source of workplace injuries. As per reports, thousands of injuries annually related to material handling equipment.
Conveyor-related accidents, such as entanglement, falls, and equipment failures, can lead to injuries. Implementing safety standards ensures compliance with legal requirements and also protects employees.
For employers, fostering a culture of safety is a regulatory requirement and a moral obligation. It demonstrates care for employees and prevents costly downtime and liabilities. Let’s explore the essential safety standards for warehouse conveyors that every facility should implement.
How can you prevent mishaps
By adhering to safety standards, warehouses can:
- Prevent accidents and injuries.
- Enhance operational efficiency.
- Avoid regulatory penalties.
- Boost employee morale and confidence.
Key Safety Standards for Warehouse Conveyors
1. Operational Safety Measures
- Workers must be trained to operate conveyors safely, especially troubleshooting.
- Cear, visible signs should warn of potential hazards. Eg. pinch points, hot surfaces, or high-speed belts.
- Non-authorized personnel should not access conveyor zones. Use barriers or restricted areas to enforce this rule.
2. General Design Standards
Safety starts at the design stage. Conveyors must be engineered with stability, durability, and compatibility with the warehouse environment. Key design standards include:
- Exposed belts, pulleys, and gears must be covered to prevent accidental contact.
- Accessible and clearly marked emergency stop buttons should be placed at regular intervals along the conveyor.
- Overloading conveyors can lead to mechanical failures. Systems must be designed to display and enforce load limits.
3. Ergonomic Considerations
Operators and workers interact with conveyor systems daily. Ensuring ergonomic designs minimizes physical strain and reduces injury risks:
- Adjustable heights for loading and unloading points
- Minimal vibration to reduce fatigue
- Adequate lighting around the conveyor area
4. Promote a Culture of Reporting Concerns
Employees are often the first to notice potential hazards. It can be loose guards or malfunctioning equipment. Encourage them to report issues without fear of repercussions.
- Establish a clear chain of communication for reporting hazards
- Provide ongoing safety training
- Act promptly on reported concerns
5. Use Signage and Warning Labels
Clearly mark hazardous areas such as pinch points and emergency stops. Visual cues like signs and labels are essential for both seasoned employees and new hires.
6. Schedule Regular Maintenance
Regular inspections can identify wear and tear, faulty components, and other issues. Hence, a well-maintained conveyor is a safe conveyor.
7. Restrict Operation to Authorized Personnel
Only trained personnel should operate or maintain conveyor systems. Improper use by untrained employees.
8. Creating a Culture of Safety
Safety is not just about policies; it’s about culture. Warehouses must encourage open communication. Employees must feel empowered to report hazards and suggest improvements. Regular safety audits, coupled with effective leadership can reinforce the message.
Conclusion
Warehouse conveyors are indispensable for efficient operations. But they must be managed with a strong focus on safety. By adhering to established standards warehouses can reduce risks.
Moreover, integrating technology while being safe ensures long-term compliance. After all, a safe warehouse is a productive warehouse. Learn more on: (link)